The company upgraded GD6# furnace, GD8# furnace, GD3# furnace, GD4# furnace one after another during the period of 2019 to 2022, the kiln was re-laid and supported with advanced bottle making system to meet the light weight production. Among them, the fuel of GD8# and GD4# furnaces was changed from petroleum coke to natural gas. After the completion of the renovation, all the kilns of the enterprise are fuelled by natural gas, and advanced kiln computer auto-control system and automatic product inspection system, self-control technology of electric and gas heating of the material channel and spraying technology of hot and cold ends, computer-controlled production line technology of three-drop material for bottles and cans, small-opening pressure blowing technology, light-weighting technology, and other advanced technologies are adopted.
The details of the project are shown in the table below.
Table 1 Project details of kiln energy-saving upgrading and renovation
serial number | Project name | Project content | Implementation time |
Investment
($ million)
| Effectiveness of implementation |
1 | GD6# Furnace Energy Saving Upgrading Project | The kiln was rebuilt with a state-of-the-art bottle-making system to meet lightweight production. | 2019.09~2020.05 | 6592 | After the implementation of the project, the melting unit consumption decreased from 159.51kgce/t to 144.24kgce/t, with an annual saving of 1,269,400m3 of natural gas, equivalent to 1,402.81tce of standard coal. |
2 | GD8# Furnace Energy Saving Upgrading Project | The kiln was rebuilt, the fuel was changed from petroleum coke to natural gas, and the production line was equipped with an advanced bottle-making system to meet lightweight production. | 2020.01~2020.06 | 5890 | After the implementation of the project, the melting of the kiln furnace was all switched to natural gas, and the melting unit consumption was reduced from 160.77kgce/t to 140.38kgce/t, with an annual saving of 1,937.39tce of standard coal. |
3 | GD4# Furnace Energy Saving Upgrading Project | The kiln was rebuilt, the fuel was changed from petroleum coke to natural gas, and the production line was equipped with an advanced bottle-making system to meet lightweight production. | 2020.01~2020.07 | 5198 | After the implementation of the project, the melting of the kiln furnace was all switched to natural gas, and the melting unit consumption decreased from 232.21kgce/t to 166.28kgce/t, with an annual saving of 3648.36tce of standard coal. |
4 | GD3# Furnace Energy Saving Upgrading Project | Furnace rebuilt with advanced bottle-making system for lightweight production | 2021.09~2022.02 | 5408 | After the implementation of the project, the melting unit consumption decreased from 157.58kgce/t to 143.42kgce/t, and the annual saving of natural gas was 899,200m3, equivalent to 1032.23tce of standard coal. |
add up the total | / | / | 23088 | The total energy saving is 8020.79tce. |
Photographs of the project implementation site are shown below.
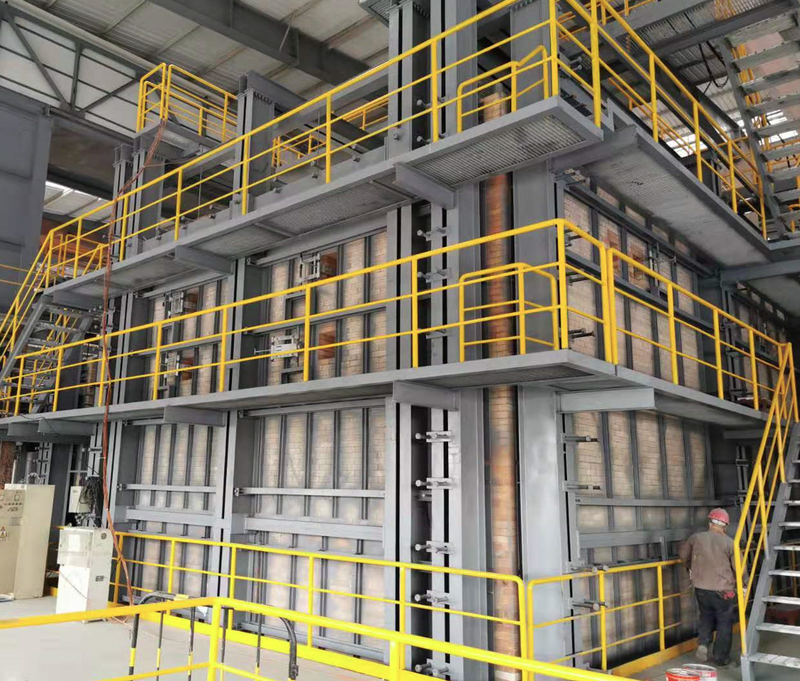
Figure 1 Photographs of the kiln energy-saving upgrading project site1
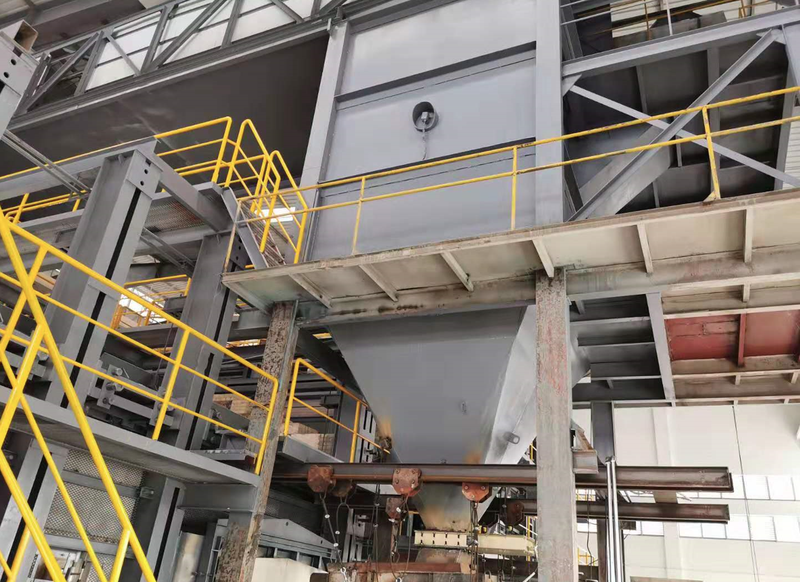
Figure 2 Photographs of the kiln energy-saving upgrading project site2
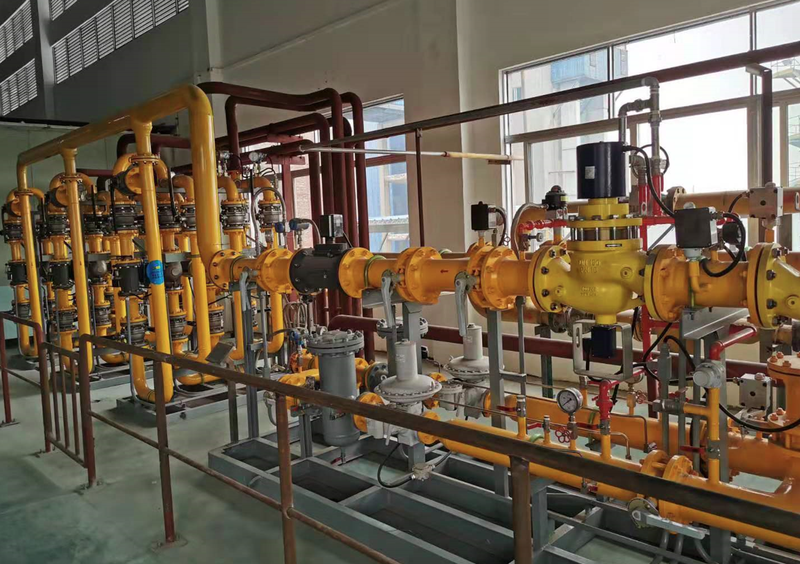
Figure 3 Photographs of the kiln energy-saving upgrading project site3
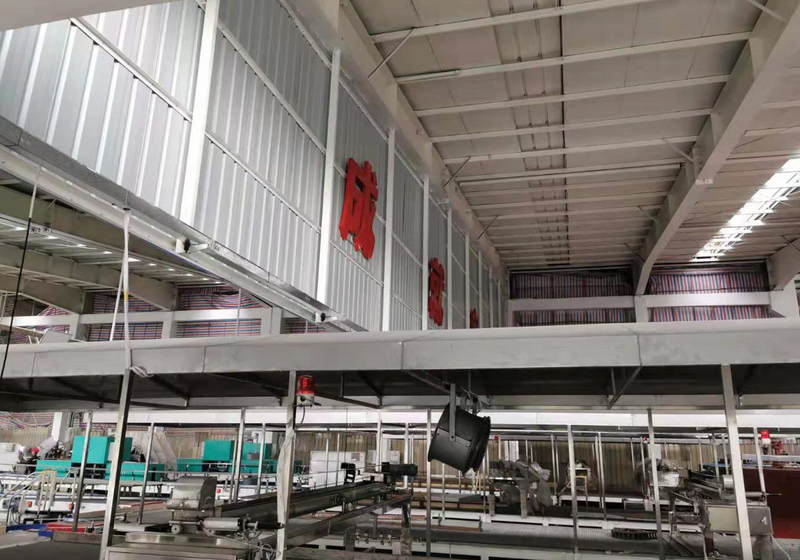
Figure 4 Photographs of the kiln energy-saving upgrading project site4